This blog post was originally posted on July 26, 2022.
Brad Wilson
19 July 2022
Brad Wilson is a process engineer working in Canada’s water and wastewater sector. As part of a commissioning team, he recently used his Pokit® Meter to diagnose and troubleshoot a malfunctioning water level sensor loop.
The sensor in question used a powered 4-20mA signal loop to relay water level readings to a programmable logic controller (PLC) nearly 700 m away. During system commissioning, induced voltages of significant magnitude were noted on the line, leading to equipment failure.
While playing out various operational scenarios, the field team used the Pokit® Meter to monitor and record electrical current and voltage on signal wires and cable shielding across several water sensors. By using the Pokit® mobile app and remotely connecting to multiple Pokit® Meters, the team could isolate and pinpoint the operational tasks causing the voltage peaks. Using the same meters in data logging mode, they could also systematically rule out the location at which the stray voltages were being generated and effectively brainstorm solutions.
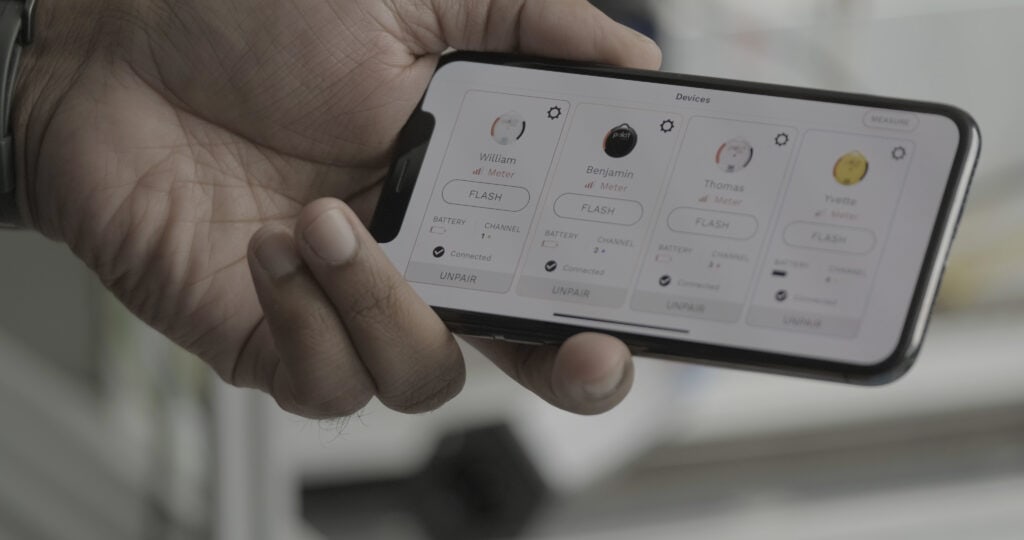
The ability to collect real-time data through the Pokit® app at various spots in the signal path enabled the team to perform equipment troubleshooting at a trivial cost. In one instance, this tool allowed on-site operators to monitor equipment performance while the sensor was physically being moved. It is estimated that without the Pokit® Meter, a C$30,000 intervention service would have been required to resolve the problem.
The data logging feature of the Pokit® technology allowed the team to perform statistical analysis and easy data presentation. It was vital for providing daily client and team updates and quickly showed the effect of any implemented solutions using the real-world (rather than simulated) data. This helped alleviate any potential “black box” thinking and gave our client much-needed confidence that our team was making progress in troubleshooting the problem.
Additionally, getting real-world instantaneous data allowed all stakeholders to discuss solutions from an easily understood common ground. This approach helped promote innovative solution development, allowing people from various technical disciplines to digest the problem and participate in simple terms. Finally, the simple Pokit® app data interface, which was quickly screenshot, saved numerous data formatting and reporting hours, culminating in project budget savings.
In summary, using Pokit® Meter was critical in diagnosing and solving the issue. Similar devices with indexed features require multiple times the capital investment. We estimate that using this meter saved nearly C$10k to C$20k in additional capital investment or specialised services, sidestepped a $C30k service call, and saved almost two full weeks of a senior engineer’s time for troubleshooting.
Pokit Meter is available for purchase via the Pokit Shop.
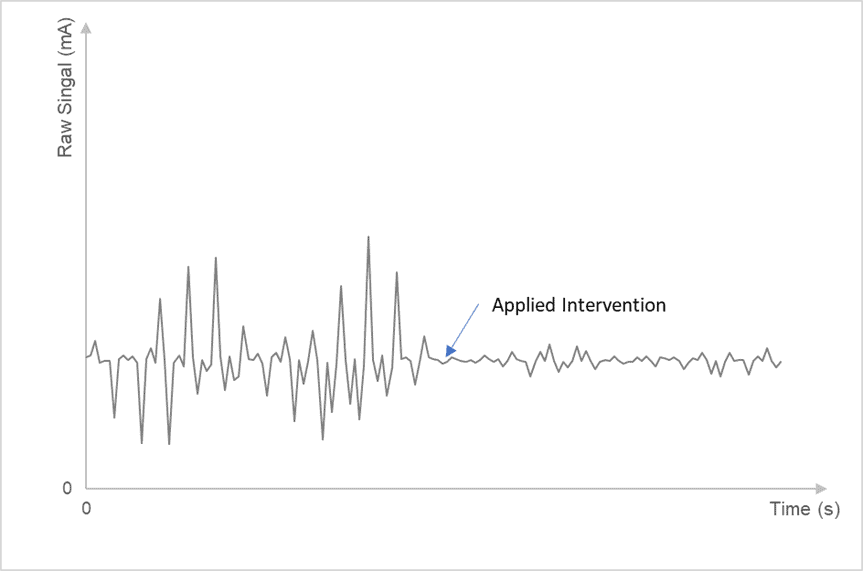
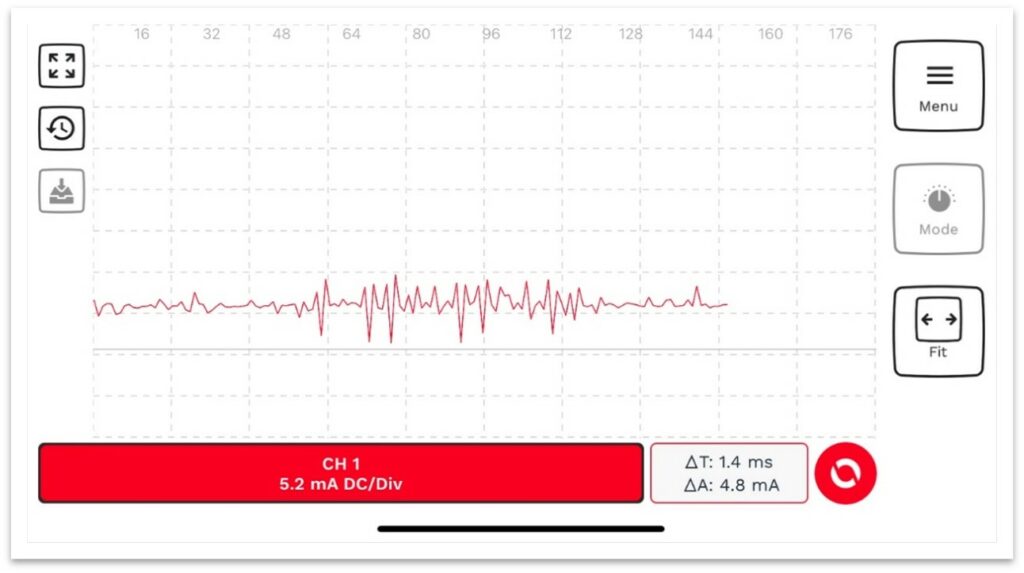
Leave a comment
This site is protected by hCaptcha and the hCaptcha Privacy Policy and Terms of Service apply.